

You can easily recognize it due to the solar cells which are in single flat color. It is also the oldest and is made out of a single continuous crystal structure. Of these three technologies this is the most developed one. Let’s present the candidates as well as their pros and cons: 1.

Thin film is totally different, less efficient but it excels in low light conditions. The first two are made out of crystalline silicon and are most common material for making solar panels. BOS components are the final step in constructing a working PV system.Ĭommercial production is currently based on three types of thin-film solar cells: amorphous silicon (a-Si), cadmium telluride (CdTe), and copper indium gallium selenide (CIGS).This article will present the three musketeers of the Solar panel world: Monocrystalline, Polycrystalline and Thin film solar cells. Multiple cells are strung together in a protective package to form a PV module interconnected modules form an array. A junction in the body of the device provides the electric field that separates and gathers the generated charge carriers, which are then collected by wires attached to the cell. When photons enter the cell through a transparent contact, they are absorbed by the semiconductor, thus creating electron-hole pairs.

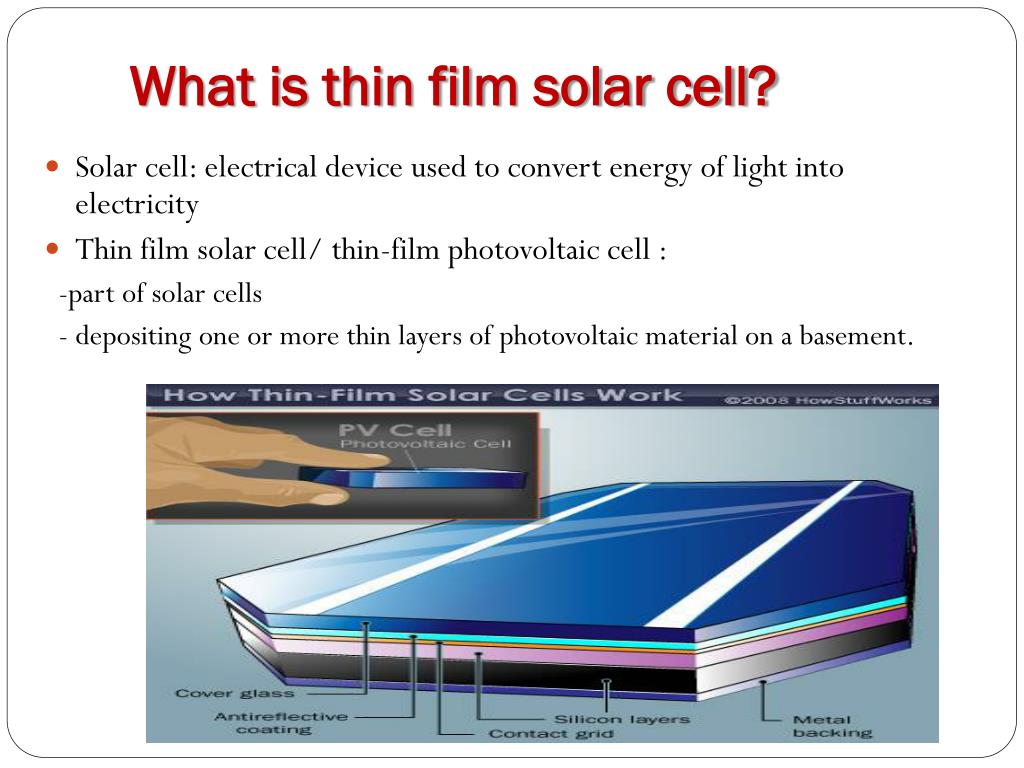
PV cells are fabricated using semiconductors as light-absorbing layers that convert the energy of photons into electricity - without noise or air pollution. Our proprietary approach embodies critical technology, manufacturing and cost advantages to enable large-scale, “fab-style” production. Thin-film solar cells employ lightweight, flexible substrates, making them ideal for advanced applications such as building-integrated photovoltaics. What’s more, because of the lightweight form factor, the costs of balance-of-system (BOS) components (such as mounting hardware, wiring, inverters and other electronic hardware) are comparatively lower than other PV devices.ĭedicated to delivering the most competitive solar cell solutions, SoloPower targets the critical challenges of producing CIGS-based devices, which have the highest conversion efficiency among the family of thin-film PVs. These cost-saving alternatives also offer another important advantage as compared to wafer-based modules in that they can be used in a wide range of applications. On the contrary, thin-film solar cells utilize only a 1-4 µm-thick layer of semiconducting material to produce electricity, thus requiring less processing and fewer materials. Typically 150 µm thick, the wafers demand multiple processing steps before they can be integrated into a module. Here’s why: the majority of solar cells in existence today are made from rigid multi- or single-crystalline silicon (Si) wafers. In developing next-generation solar alternatives, a thinner profile is paramount. We are strategically committing considerable resources and brainpower, and are poised to eliminate the gap and reach grid parity. SoloPower has developed a new solution and is introducing products that address the all-important cost factor and will allow for a wider use of solar energy. Historically, the costs of manufacturing PV cells and modules have been high, causing the cost of solar energy to be three to five times more expensive than traditional methods. The term originates from the Greek word for light, photos, combined with voltaic - in recognition to Alessandro Volta, an eighteenth-century Italian scientist who carried out pioneering studies in electricity. Photovoltaic, or PV, refers to the conversion of light energy into electricity using electronic devices called solar cells. SoloPower Systems leads the way with a line of thin-film photovoltaic solar cells that adapt to virtually limitless site-specific applications. Innovations once only imagined in the solar industry now set the standard for generating highly efficient, low-cost energy.
